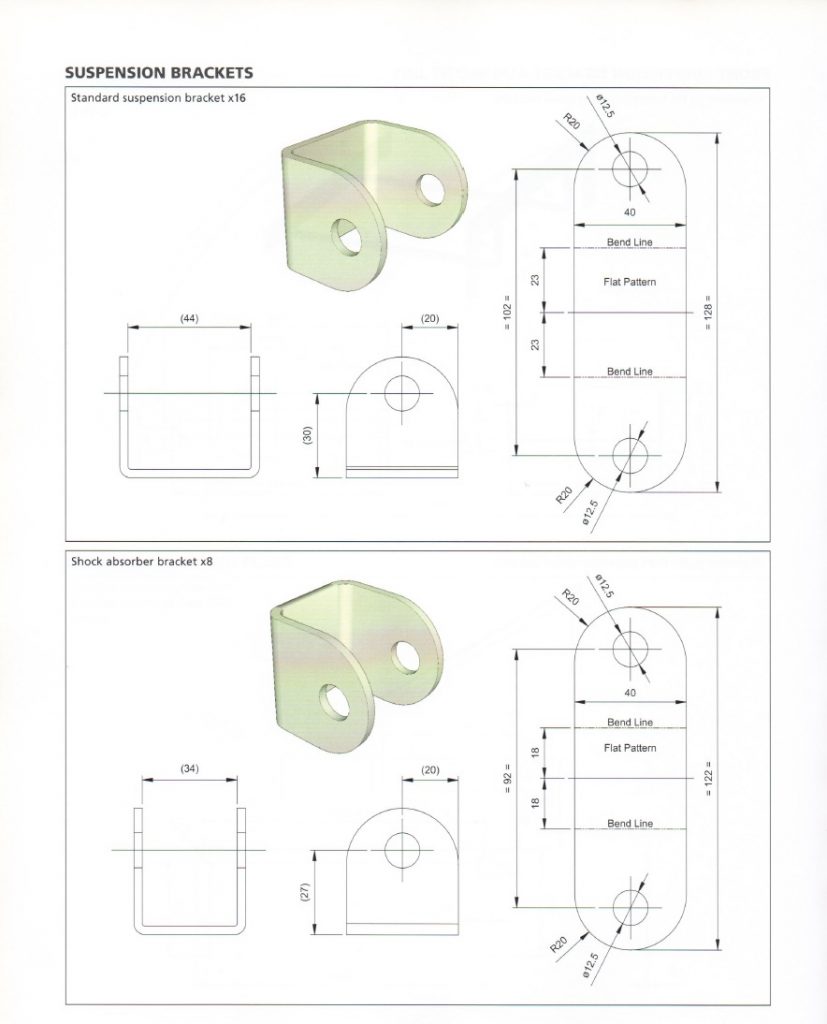
We need brackets in order to proceed. There are 8 shock brackets and 16 suspension brackets used in the build. The shock mounts are needed to fabricate the back framework of the car. It is possible to buy brackets but what would be the fun in that? This is another opportunity to use that hydraulic press.
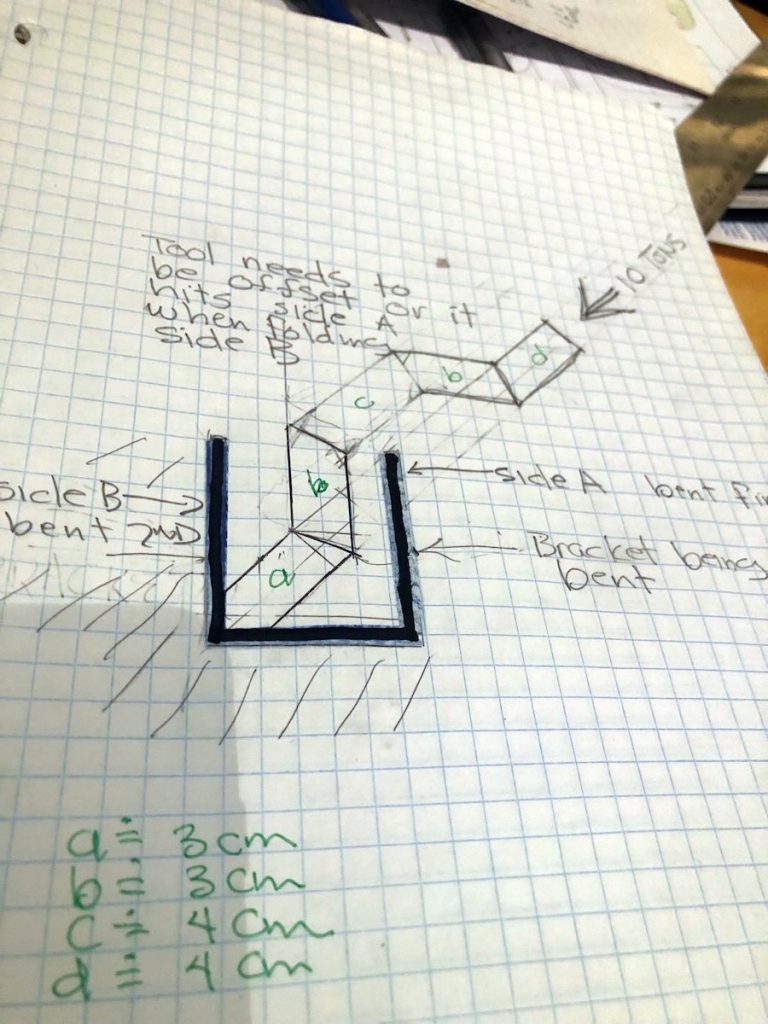
In order to make U shaped brackets we need a “press break”. The break has two parts, a punch and die and in our case they will both be 90 degrees. The punch is forced into the die pressing the metal to be bent forming a right angle. Now we have “L” shaped brackets. Then we put the straight end of the “L” on the die and press it to form a “U” shape. The punch will need to have an offset so that the second fold does not cause the first folded side to interfere with it. This is another of my detail “design drawings” that shows how the punch needs to be shaped.
The punch was made from 1/2″ steel. The chop saw cuts it easily, the parts were cleaned up with the angle grinder giving the edges a bit of a bevel so hopefully the weld penetrates better.
After it was fully welded I made a collar to attach it to the hydraulic cylinder and welded that on.
I had a couple different dimensions of thick walled square tube and thought I could make the die from that. It also gave me more practice welding. Once that was done I put a test bracket in the press to see if it would work.
Bending both sides of the bracket. You can see why the offset is needed.
This worked surprisingly well, the 1/8″ steel folded like paper in the press. There was negligible pressure on the hydraulic gauge until the punch bottomed out in the die. When that happened I pumped the press handle and put about 2 tons force into the die. The result was that the bends were a bit over 90 degrees. The bottoming out pressure really seems to set the angle, too little and it is a bit under 90 too much and it is a bit over. Some experimentation required.
The two dies that I made would not be useful for producing all the brackets needed. There was no way to easily position blanks on the die consistently in order to get repeatable results. I would have to make a better die.
I did some Google research and found that having the throat width of the die equal 8 times the material thickness being bent is ideal. Since I was bending 1/8″ material a 1″ throat would be needed. Math reared it’s head again, I still had some 1/2″ thick bar and cutting 45 degrees to make the die would make a throat width of exactly 1″. The chop saw did it’s thing and this time I just tacked the plates together. The flat bed allowed me to clamp a stop block down and position the blanks consistently.
I made up the 8 blanks for the shock mounts and used a template to drill pilot holes in each end before drilling them to 1/2″. I then bolted them all together and used the angle grinder to round the ends. Now I unbolted the blanks and started bending.
Half way done. The finished product.
That worked out great. I have some ideas to improve my bracket production process that I will try on the suspension brackets. Now I need to get back to the car frame, the suspension brackets can wait till they are needed.